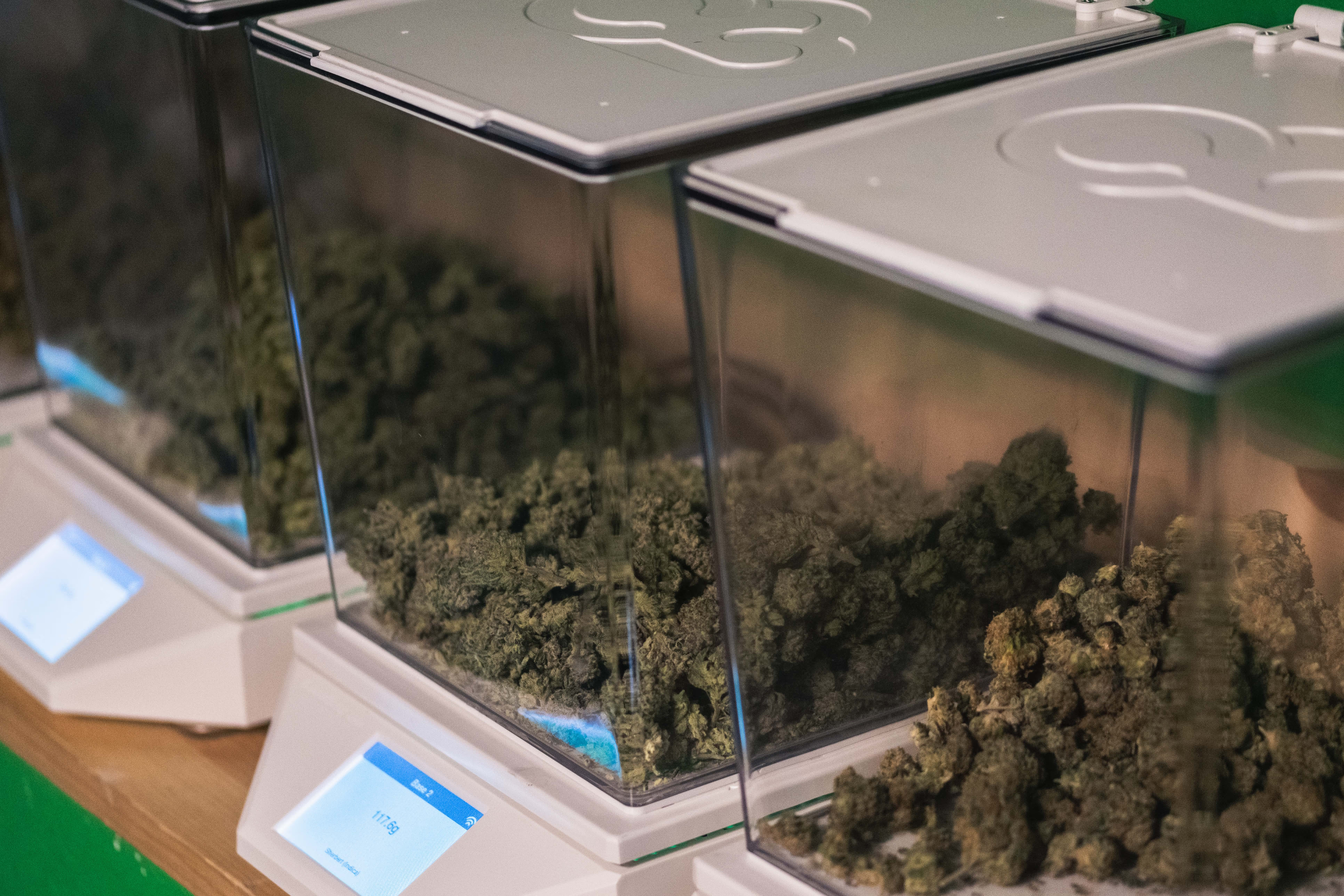
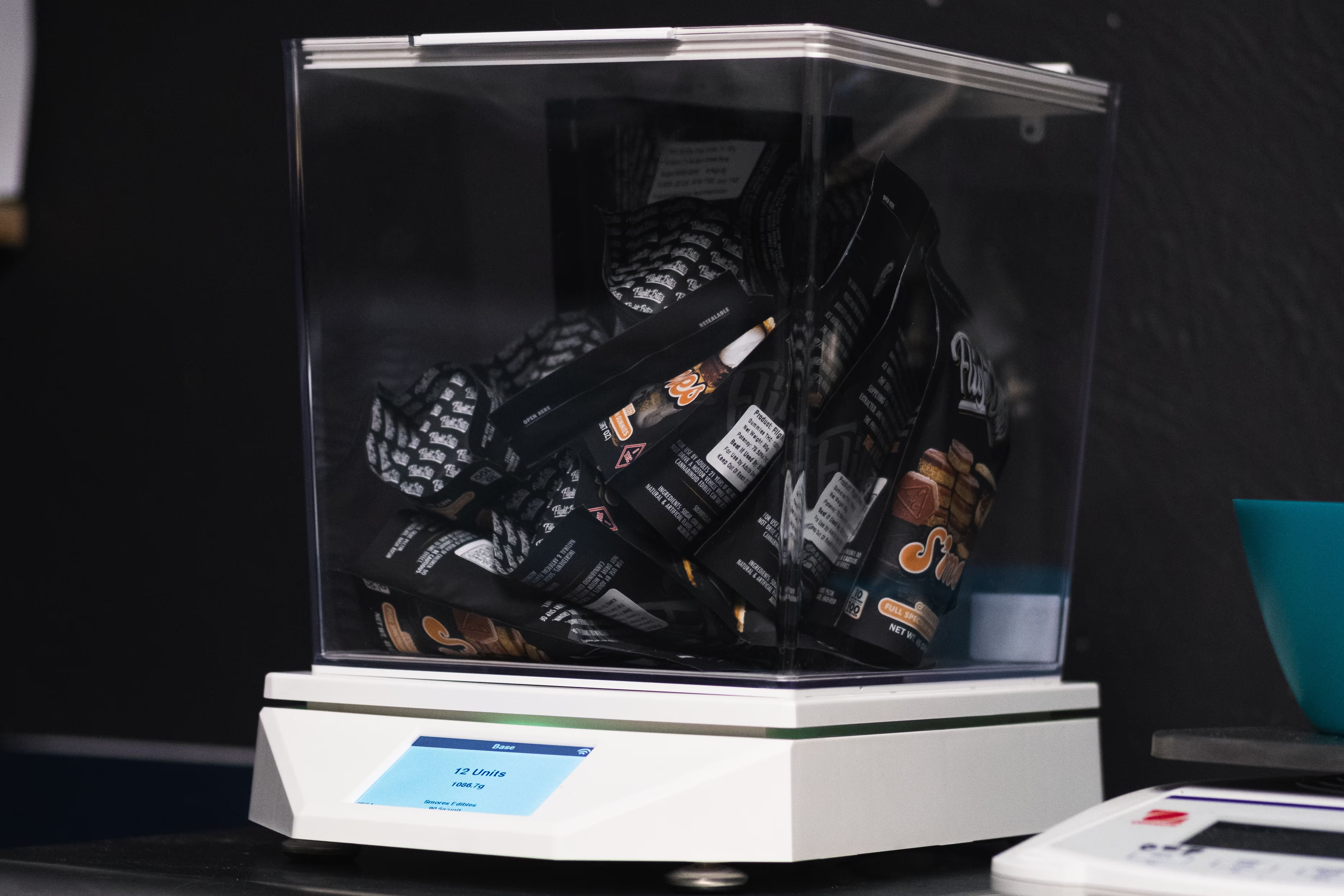
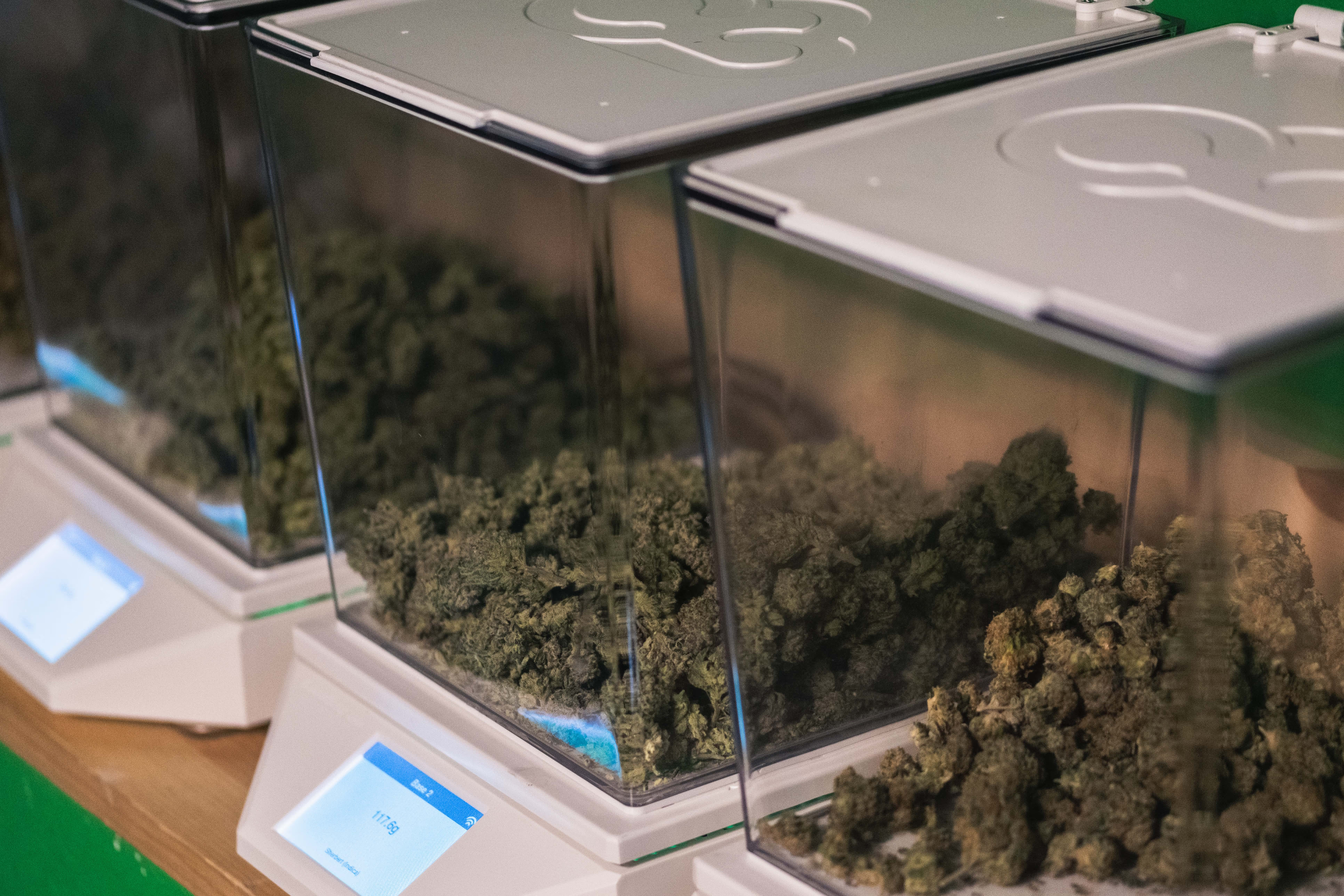
Automatically count your dispensary's inventory in real-time, eliminating theft/shrinkage & saving thousands on compliance.
Inventory that is removed or added will updated in real-time on our web portal and mobile app.
CloudBox verifies if inventory transactions were sold at the Point-Of-Sale (POS) and determines if it was stolen/shrinkage.
Send your inventory directly to BioTrack & METRC with a click of a button.
Perfect for deli-style or prepackaged goods, CloudBox can be customized to fit any business's model.
CloudBox's advanced analytic dashboard tracks inventory changes in real-time. This allows businesses to make more informed decisions on consumer preferences, inventory shrinkage, and predictive market trends.
Set dynamic inventory alerts to be notified when certain thresholds are met. Cannabis businesses can be notified when to reorder inventory, when theft occurs, and if there is inventory is in your CloudBox that shouldn't be there.
CloudBox container modules track the content's inventory data allowing any container to be used with any base. Simply replace your old containers with CloudBox container modules let the base do the rest!
EzAds is a powerful, user-friendly Ads Manager dashboard that helps you easily manage, track, and optimize your advertising campaigns across multiple platforms in one place. With EzAds, you can streamline your ad operations, analyze performance in real-time, and improve your overall advertising results.
Yes! EzAds is designed with simplicity in mind. Its intuitive interface allows even non-experts to manage complex ad campaigns without a steep learning curve. Whether you're a beginner or an experienced marketer, EzAds provides an easy-to-use platform that helps you stay in control.
Yes! You can enjoy a 7-day free trial when you sign up for EzAds. This gives you a chance to explore all the features and see how EzAds can improve your advertising efforts before committing to a subscription.
EzAds offers flexible pricing plans based on your needs. After your 7-day free trial, you can choose from various subscription options designed for businesses of all sizes. For more detailed pricing information, please visit our pricing page on the website.
Yes, EzAds is fully mobile-friendly! You can manage your ad campaigns, view reports, and make adjustments on the go using your smartphone or tablet.